3D Printing technology, also known as Additive Manufacturing (AM), refers to processes used to generate a 3D object in which layers of material are
successively formed under a computer controlled program to create a physical object. The 3D file source is usually sliced into several layers, each layer generating a set of computer controlled instructions.
Both 3D printing and additive manufacturing reflect that the technologies share the theme of sequential-layer material addition or joining throughout a 3D work. 3D printing technologies can be split up into 2 groups: direct
and indirect 3D printing. The main difference lies in the fact that the design is directly made from 3D printing (direct) or 3D printing was used in the process of creating your model (indirect).
The objects manufactured through 3D printing processes can be of almost any shape or geometry.
They are typically produced using digital model data from a 3D model or another electronic data source such as a STereoLithography (STL) file, one of the most common file types that 3D printers can read. The term 3D printing originally referred to a process that deposited a binder material onto a powder bed with inkjet printer heads layer by layer. More recently, the term 3D printing is being used in popular vernacular to encompass a wider variety of additive manufacturing techniques. For professionals, the additive manufacturing name remains more popular for its broader sense and longer existence. Other terms are also employed, such as desktop manufacturing, rapid manufacturing, direct digital manufacturing, and rapid prototyping.
Additive manufacturing invention can be traced back to the 1980’s by Japanese, French and American researchers. The very first patent of 3D printing was coined in 1984 by Chuck Hull of 3D Systems Corporation. Hull defined the 3D printing process as a system for generating three-dimensional objects by creating a cross-sectional pattern of the object to be
formed. His invention consists of a stereolithography fabrication system, in which layers are added by curing photopolymers with ultraviolet light lasers.
Stereolithography is still one very popular 3D printing manufacturing technique, also known as SLA. Yet, the technology used by most 3D printers in the 2010’s, especially by hobbyist and consumer-oriented products, is Fused Filament Fabrication (FFF), also known as material extrusion or the proprietary Stratasys denomination’s Fused Deposition Modeling (FDM).
FDM was patented in 1989 by S. Scott Crump just before he launched the Stratasys company with his wife, Lisa Crump.
Metal 3D printing only became available in the 1990’s with the invention of laser melting and sintering techniques. Selective Laser Sintering (SLS) and Selective Laser Melting (SLM) are often grouped under the umbrella term Direct Metal Laser Sintering (DMLS).
ISO/ASTM52900-15 defines seven categories of Additive Manufacturing (AM) processes:
Material extrusion
Photopolymerization
Powder bed fusion
Material jetting
Binder jetting
Sheet lamination
Directed energy deposition
The possibilities with 3D Printing are boundless and encompass numerous industries from plastics and metals up to organic materials and food. A broad range of materials is used in 3D Printing. Each one carefully corresponds to the technical requirements of the end product and is usually fitted for only a restrictive set of additive manufacturing technologies.
In order to illustrate the vast potential for 3D Printing, it is necessary to get a basic understanding for the most popular materials. Let’s begin with sintered powdered metal, which is used for printing the injection molds used in classic manufacturing like casting, as well as for injection molding and carbon fiber lay-up. Stainless steel, bronze, steel, gold, nickel steel, aluminum, and titanium are just a few of the suitable metals for 3D printing. These metals are particularly well suited for prototyping, jewelry, and tailored objects. Furthermore, Nitonol, an alloy of nickel and titanium, is delivering a promising outlook for the medical implant industry. Its superelasticity and ability to change shapes are two features that astonish the scientific community.
A significantly broad spectrum of plastics offers an extensive field of possibilities for 3D Printing. Far from an exhaustive list, some possible plastics include acrylics, polyamides, ABS plastic, assorted polyurethanes, epoxy resins, nylon, and PEBA 2301.
These plastics offer a plethora of conceivable objects such as prototypes, gear systems, ornaments, or educational modeling. Additionally, wax can be used for design verification, functional testing, and fine feature details. Wax is also used as a smooth surface finish and in molds for tooling.
Carbon fiber and composites are cutting-edge materials that offer a fast way of producing an object that is as strong or stronger than metal. They are most commonly employed in the bicycle and aeronautics industries.
Graphene, an allotrope of carbon, is the strongest material ever tested. It has the potential to create totally new technologies, thanks, in part, to its efficient heat and electrical conductivity as well as its near transparent appearance.
Some of the more unusual materials encompass stem cells, paper, concrete, food, and yarn. As difficult as it may be to imagine, the 3D Printing of stem cells is a showstopper in 3D Printing technology. It would make it possible to print tissues, organs, or bones that go on to be implanted into a patient.
Material extrusion technology – FDM
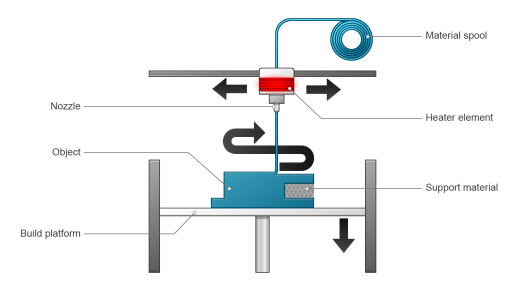
Material Extrusion 3D printing technology uses a continuous filament of a thermoplastic material as a base material.
The filament is fed from a coil, through a moving heated printer extruder head, often abbreviated as an extruder. The molten material is forced out of the extruder’s nozzle and is deposited first onto a 3D printing platform, which can be heated for extra adhesion. Once the first layer is completed, the extruder and the platform are parted away in one step, and the second layer can then be directly deposited onto the growing workpiece. The extruder head is moved under computer control. At least three axes are required for the extruder to move in Cartesian architectures, but polar and
delta systems are also becoming increasingly popular. One layer is deposited on top of a previous layer until the object’s fabrication is complete.
Material extrusion is known as Fused Filament Fabrication (FFF) and is one of the most popular processes for hobbyistgrade 3D printing. The roprietary term Fused Deposition Modeling (FDM) was coined by S. Scott Crump in the late 1980’s and was commercialized in 1990 by the Stratasys company. With the expiration of this technology’s patent, there is now a large open-source development community called RepRap, as well as commercial and DIY variants, which utilize this type of 3D printing technology. This has led to a measurable price decrease. However, the material extrusion technique has dimensional accuracy limitations and is very anisotropic.
A wide variety of materials can be extruded, the most popular being thermoplastics, such as Acrylonitrile Butadiene Styrene (ABS), PolyLactic Acid (PLA), High-Impact Polystyrene (HIPS), Thermoplastic PolyUrethane (TPU), aliphatic PolyAmides (PA, also known as Nylon), and more recently high performance plastics such as PolyEther Ether Ketone PEEK or PolyEtherimide PEI. Additionally, paste-like materials such as ceramics, concrete and chocolate can be extruded using this 3D printing technique.
As it became possible to equip a 3D printer with multiple extruders, for speeding up the fabrication process or opening multi-material capabilities, the availability of composite fabrication became possible. Composite Filament Fabrication (CFF) is one of them. This term was coined by the company Markforged and uses two print nozzles. One nozzle operates
following the typical material extrusion process; it lays down a plastic filament that forms the outer shell and the internal matrix of the part. The second nozzle deposits a continuous strand of composite fiber (made with carbon, fiberglass, or Kevlar) on every layer. These continuous strands of composite fibers inside 3D printed parts add a strength to the built
object that is comparable to parts made of metal. In addition to using composite materials for strong parts, the strategy used to lay down layers can affect part strength. Markforged distinguishes two strategies: isotropic fiber fill or concentric fiber fill.
Even composites can be 3D printed with the material extrusion technique on machines equipped with only one extruder.
The sole condition is that the base material (a thermoplastic) is present in sufficient quantities to guarantee a fusion between layers. Therefore, a mix of two materials within a single filament made wood 3D printing (wood particles embedded in PLA), metal 3D printing (metal particles embedded in thermoplastic) and even carbon 3D printing (carbon fibers embedded in thermoplastic) possible.