Bending is one of the most common sheet metal fabrication operations. Also known as press braking, flanging, die bending, folding and edging, this method is used to deform a material to an angular shape. This is done through the application of force on a workpiece.
The force must exceed the material’s yield strength to achieve a plastic deformation. Only then can you get a lasting result in the form of a bend. What are the most common bending methods? How does springback
affect bending? What is k factor? How to calculate bend allowance? All those questions are discussed in this article along with some bending tips.
Bending Methods:
There’s quite a few different bending methods available. Each has their own advantages. The dilemma is usually between going for accuracy or simplicity, while the latter gets more usage. Simpler methods are more flexible and most importantly, need less different tools for getting a result.
V-Bending:
V-bending is the most common bending method using a punch and die. It has three subgroups – bottoming air bending and coining. Air bending and bottoming account for around 90% of all bending jobs.
The table below helps you identify the minimum flange length b (mm) and inside radii ir (mm) according to material thickness t (mm). You can also see the die width V (mm) that is needed for such specifications.
Each operation needs a certain tonnage per meter. This is also shown in the table. You can see that thicker materials and smaller inside radii require more force, or tonnage. The highlighted options are recommended
specifications for metal bending.
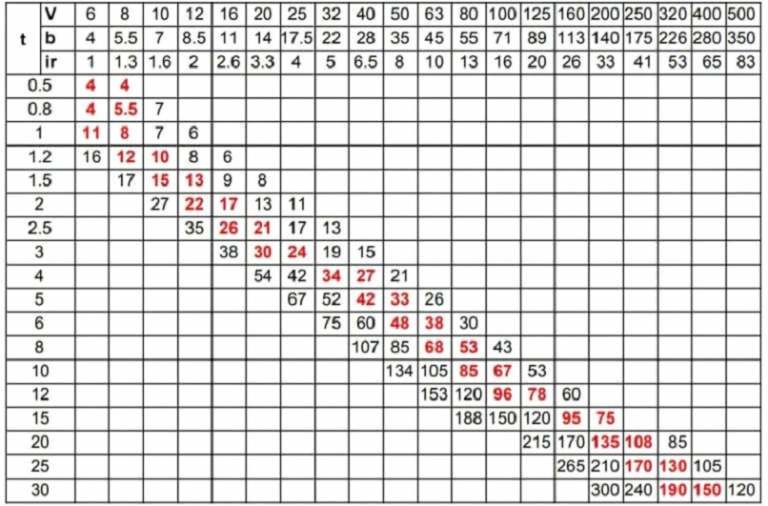
Let’s say I have a 2 mm thick sheet and I want to bend it. To keep it simple, I also use a 2 mm inside radius. I can now see that the minimum flange length is 8.5 mm for such a bend, so I have to keep it in mind when
designing. The required die width is 12 mm and tonnage per meter is 22. The lowest common bench capacity is around 100 tonnes. My workpiece’s bending line is 3 m, so the overall needed force is 3*22=66 tonnes.
Therefore, even a simple bench with enough room to bend 3 m pieces will do the job. Still, there is one thing to keep in mind. This table applies to construction steels with a yield strength around 400 MPa. When you want to bend aluminium, the tonnage value can be divided by 2, as it needs less force. The opposite happens with stainless steel – the required force is 1.7x higher than the ones displayed in this table.
Bottoming:
Bottoming is also known as bottom pressing or bottom striking. As the name “bottom pressing” suggests, the punch presses the metal sheet onto the surface of the die, so the die’s angle determines the final angle of the
workpiece. With bottoming, the inner radius of the angled sheet depends on the die’s radius. As the inner line gets compressed, it needs more and more force to further manipulate it. Bottoming makes exerting this force possible, as the final angle is preset. The possibility to use more force lessens the spring back effect and provides good precision.
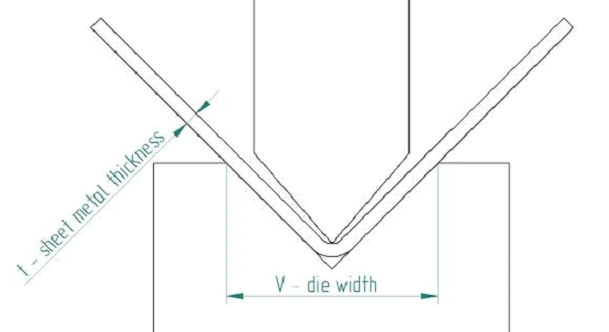
The angle difference accounts for the spring back effect When bottoming, an important step is calculating the Vdie opening.
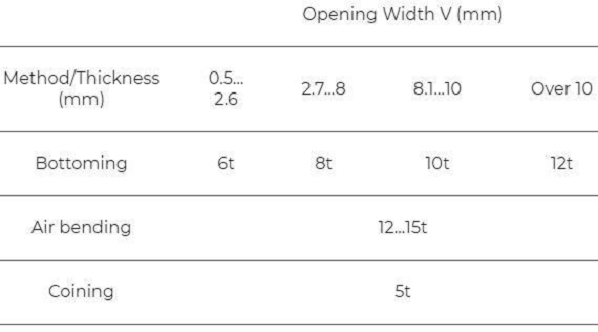
The inner radius has been experimentally proven to be around 1/6 of the opening width, meaning the equation looks like this: ir=V/6.
Air Bending:
Partial bending, or air bending, derives its name from the fact that the working piece does not actually touch the tooling parts entirely. In partial bending, the workpiece rests on 2 points and the punch pushes the
bend. Is still usually done with a press brake but there is no actual need for a sided die.
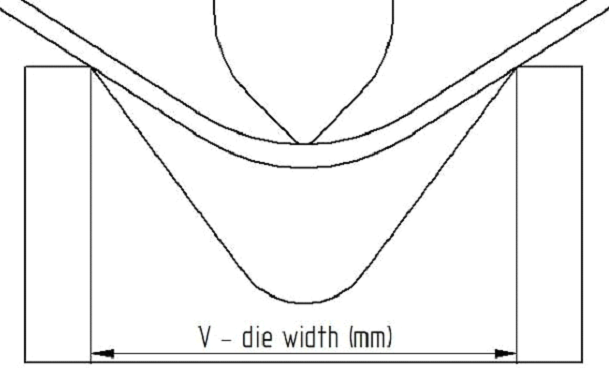
Air bending gives much flexibility. Let’s say you have a 90° die and punch. With this method, you can get a result anywhere between 90 and 180 degrees. Though less accurate than bottoming or coining, this kind of
simplicity is the beauty of the method. In case the load is released and the material’s springback results in a wrong angle, it is simple to adjust by just applying some more pressure. Of course, this is a result of lessened
accuracy compared to bottoming. At the same time, partial bending’s big advantage is that no retooling is necessary for different angle bends.
Coining:
Coining used to be far more widely spread. It was pretty much the only way to get accurate results. Today, machinery is so well controllable and precise, that such methods are not widely used any more.
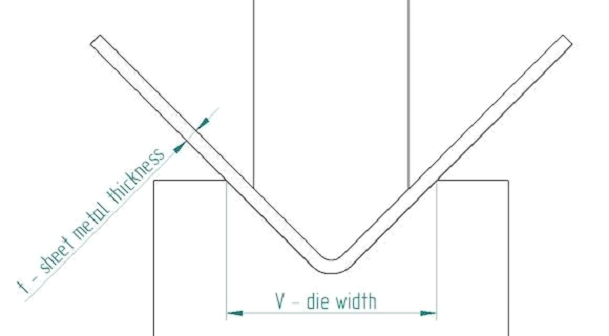
The metal is given the die’s exact shape by applying great tonnage. Coining derives it name from coins, as they have to be identical to make fake money distinguishable from the real one. Coining, in bending, gives similarly precise results. For instance, if you want to get a 45 degree angle, you need a punch and a die with the exact same angle. There is no springback to
worry about. Why? Because the die penetrates into the sheet, pressing a dent into the workpiece. This, along with the high forces used (about 5-8 times as much as in partial bending), guarantee high precision. The
penetrating effect also ensures a very small inside radius for the bend.
U-Bending:
U-bending is in principle very similar to V-bending. There is a die and a punch, this time they are both Ushaped, resulting in a similar bend. This is a very straightforward way for bending steel U-channels, for example, but not so common as such profiles can also be produced using other more flexible methods.