برخی از مهندسان و طراحان در طراحی یک قطعه یا پروژه ورق کاری و خمکاری مشکلات زیادی را تا پایان تولید یک محصول پیش روی خود دارند. بیشتر این مشکلات از مرحله طراحی یک پروژه ورق کاری نشات گرفته که تولید یک محصول را به شدت تحت تاثیر قرار می دهد. با توجه با این موضوع، به توضیح برخی از موارد که رعایت آنها می تواند باعث بهبود کیفیت یک پروژه ورق کاری شود، می پردازیم.
حداقل طول یک لبه یا فلنج:
در هر کارگاه یا کارخانه ساخت و تولید، ماشین آلات و ابزارهای متفاوتی وجود دارد. با توجه به این موضوع و بر اساس پتانسیل های ساخت برای خمکاری هر لبه یا فلنج یک حداقل مقداری وجود دارد. برای این منظور به نمودار مقدار نیروهای خمش برای هر فلنج مراجعه کرد. با توجه به ضخامت، عرض قالب را انتخاب نمایید. سپس با توجه به شرایط موجود ارتفاع فلنج خود را طراحی نمایید. اگر یک فلنج خیلی کوتاه طراحی کنید، به طرز نامناسبی درون شکاف ماتریس می افتد و نتیجه مطلوب بدست نخواهد آمد.
گوشه های پخ خورده:
پخ هایی که در گوشه های قطعه طراحی می شوند نباید تا انتها و قسمت خط خم برسند. باید قبل از آن متوقف شوند. اگر میخواهید فلنج یا لبه ای طراحی کنید که یک یا هر دو سمت آن دارای پخ می باشد باید قانون قبل یعنی درنظر گرفتن طول یک فلنج را طوری رعایت نمایید که در انتهای پخ این مقدار وجود داشته باشد. در غیر اینصورت و درصورتی که پخ تا انتها ادامه داشته باشد در هنگام خمکاری دچار دفرمگی شده و نتیجه مطلوبی بدست نخواهد آمد.
فاصله سوراخ ها و شکاف ها از لبه خم:
سوراخ ها و شکاف های نزدیک به قسمت خمکاری ممکن است دچار پیچش و دفرمگی شوند. ممکن است این مشکل در ظاهر نیز بسیار نمایان نباشد. اما ممکن است باعث شود تا پیچ ها، مهره ها یا پرچ های شما به درستی در جای خود قرار نگیرند. برای جلوگیری از این مشکل با توجه به حداقل طول یک فلنج، سوراخ ها را در فاصله ای بیشتر از آن طراحی نمایید.
تقارن:
سوراخ مستطیل شکل می تواند در دو طرف باشد. این یک اشتباه بزرگ است که در ساخت قطعاتی که تقریبا متقارن هستن می تواند رخ دهد. در صورت امکان بهتر است قطعه بصورت متقارن طراحی شود و یک سوراخ مستطیل شکل دیگر نیز به صورت متقارن در قسمت رو به رو ایجاد گردد. در غیر اینصورت در صورتی که قطعه تا حد زیادی متقارن بوده و تنها در برخی جزئیات دارای تفاوت باشد. ممکن است باعث اشتباه و سردرگمی اپراتور دستگاه شود و قطعه کار در جهت خالف و نادرست خمکاری شود. برای جلوگیری از بروز این مشکل حتما و به صورت واضح در نقشه توضیحات لازم را ذکر نمایید و درصورت امکان اپراتور را متوجه جزئیات بگردانید.
مهره های پرچی:
معمولا بهتر است مهره های پرچی ای که نزدیک محل خم هستند قبل از خمکاری پرچ شوند. زیرا ممکن است بعد از خمکاری سوراخ نشیمن آنها روی ورق به دلیل نزدیکی به موقعیت خم دچار کشیدگی یا دفرمگی شود. در اینصورت حتما چک نمایید که ابزار خمکاری به این مهره ها برخوردی نداشته باشد. در صورت برخورد، اجتناب ناپذیر است که ابتدا عملیات خمکاری را انجام داده و سپس مهره ها را درون موقعیت خود پرچ نمایید.
لبه ها و فلنج های کوچک بر روی قطعات بزرگ:
یک خم کوچک در انتهای یک قسمت بزرگ ممکن است باعث بروز مشکلاتی شود. بهتر است فلنج های کوچک بر روی قطعات بزرگ و سنگین حذف شوند. وجود چنین لبه هایی فرآیند تولید را بسیار دشوار کرده و ممکن است نیاز به خمکاری دستی یا استفاده از سایر فرآیند ساخت و تولید باشد. ممکن است ضمن پایین آمدن دقت کار هزینه ساخت آن نیز بسیار افزایش یابد. بدین ترتیب بهتر است این موضوع را در طراحی در نظر داشت.
خم های متوالی:
همانطور که در قسمت های قبلی ذکر شد، هرکارگاه یا کارخانه ساخت و تولید ماشین آلات و ابزار آلات مشخصی دارد. در صورت طراحی قطعات دارای خم های متوالی ابتدا از پتانسیل های موجود در کارگاه مطلع شوید. سپس فاصله و جهت خم های متوالی از هم را تعیین نمایید.
طراحی خط های خم در یک ردیف:
در صورتی که چندین فلنج پشت سر هم داشته باشید، بهتر است خم ها را روی یک خط قرار دهید. بدین صورت می توانید تعداد عملیات های ساخت را به حداقل برسانید. در غیر این صورت، اپراتور باید قطعات و دستگاه را برای هر خم مجدد تنظیم کند، که سبب افزایش زمان و هزینه تولید می شود.
خط خم موازی با لبه:
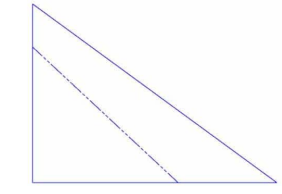
خم ها را به گونه ای طراحی کنید که خط خم موازی با لبه قطعه باشد. در غیر اینصورت قرار دادن قطعه در موقعیت مناسب خمکاری بسیار دشوار بوده و ممکن است قطعه دچار خطا گردید و نتیجه نهایی مطلوب نباشد.
فضای خالی انتهای خم:
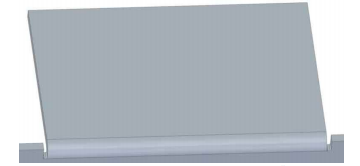
برای به دست آوردن بهترین نتیجه در خم، توصیه می شود که نه تنها یک برش لیزر کوچک، بلکه یک فضای خالی واقعی در دو طرف فلنج قرار دهید. بهتر است عرض این فضای خالی بیشتر از ضخامت ورق درنظر گرفته شود. با این کار می توان مطمئن بود هیچگونه پارگی یا دفرمگی در قسمت های انتهایی خم ها ایجاد نمی شود. همچنین می توان برای بهبود تمرکز تنش در این نواحی بجای شیار، نیم دایره های کوچکی ایجاد کرد.
خمکاری یک جعبه:
هنگام خمکاری یک جعبه، بهتر است فاصله های بسیار کمی بین فلنج ها یا همان لبه ها ایجاد شود. در غیر این صورت ممکن است آخرین خم، به خم های دیگر برخورد کرده و باعث دفرمگی و لهیدگی قطعه شود.
گسترده قطعه را بررسی کنید:
در هنگام طراحی یک قطعه خمکاری پس از طراحی هر قسمت مدل سه بعدی خود را به حالت گسترده درآورده و گسترده مدل را در هر مرحله بررسی کنید. ممکن است مشکلاتی را در هر قسمت مشاهده نمایید که در مدل سه بعدی قابل رویت نباشد. بعضا شاهد برخورد دو لبه و افتادگی دو قسمت روی هم در حالت گسترده مدل هستیم. که این مشکل در هنگامی که مدل حالت سه بعدی دارد قابل مشاهده نخواهد بود. همچنین بسیار پیش آمده است که با بررسی ابعادی گسترده یک قطعه و تنها کاهش 1 یا 2 میلیمتری ابعاد، توانسته ایم. قطعه را در هنگام برش لیزر بر روی ورق استاندارد کوچکتری قرار دهیم. که سبب کاهش هزینه های تولید گردیده است.
تعیین شعاع خم به اندازه ضخامت ورق:
در طراحی یک قطعه خمکاری بهترین کار تعیین شعاع داخلی خم به اندازه ضخامت ورق است. در نظر گرفتن شعاع خم کمتر از ضخامت ورق مشکلات بسیاری را ایجاد می کند و در نظر گرفتن شعاع خم بیش از ضخامت ورق محاسبات بعدی را بسیار پیچیده خواهد کرد.
تعیین جهت خم:
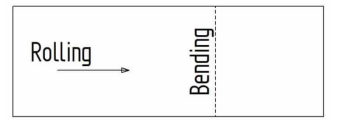
شناخت مواد اولیه:
بطور کلی مواد اولیه تولیدی از سوی کارخانه های سازنده دارای استانداردها و مشخصاتی هستند که توسط آنها شناخته می شوند. در ساخت محصولات با یک استاندارد یکسان، بعضا مشاهده شده است مواد اولیه تولیدی کارخانه های متفاوت، رفتار متفاوتی را در هنگام فرآیند خمکاری نشان می دهند. رفتارهایی از جمله آنها میتوان به کشش های متفاوت در هنگام خمکاری اشاره کرد. بعضا با توجه به یکسان بودن استحکام و حتی ترکیبات شیمیایی یک محصول از دو کارخانه متفاوت تامین کننده توصیه به استفاده یک محصول برای یک روش تولیدی خاص نمی کند. در نتیجه در هنگام ساخت یک محصول یکی از مهمترین موارد شناخت خوب و کامل مواد اولیه مورد استفاده برای روش و پروسه های تولیدی مورد نظر در جهت ساخت یک محصول با کیفیت می باشد.